Prozessoptimierung durch Value Stream Mapping und Root Cause Analyse - Qualitätssicherung bei Gislaved Folie
- Ralf Pühler
- 10. Okt. 2024
- 3 Min. Lesezeit
Bei einem unserer jüngsten Projekte arbeitete Lean-IQ mit Gislaved Folie, einem führenden Hersteller von Kunststofffolien, zusammen. Ausgangspunkt für das Projekt waren Auffälligkeiten in der Qualitätssicherung an einer Kalander-Anlage. Diese Herausforderungen boten die Gelegenheit, nicht nur den bestehenden Prozess genauer unter die Lupe zu nehmen, sondern auch die Effizienz der Abläufe signifikant zu steigern.
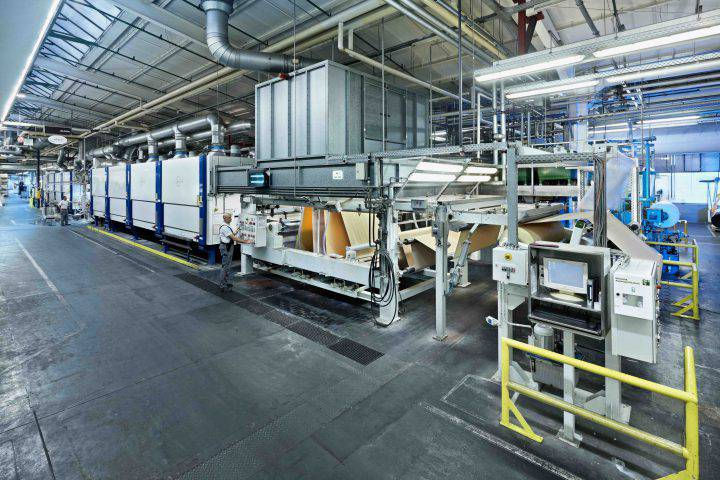
Ausgangslage: Qualitätsmängel an der Kalander-Anlage
Die Kalander-Anlage von Gislaved Folie, die in der Produktion hochwertiger Kunststofffolien eine Schlüsselrolle spielt, zeigte wiederholt Fehlstellen in den Endprodukten. Um diese Herausforderungen zu bewältigen, begann Lean-IQ mit einer Detailaufnahme aller relevanten Prozesse, die sowohl die Inbetriebnahme der Anlage als auch den operativen Betrieb umfasste. Ein Value Stream Mapping (Wertstromanalyse) diente als Grundlage, um die Prozesse zu verstehen und Verbesserungspotenziale zu identifizieren.
Untersuchungen im Labor: Fehlstellen analysieren
Neben der Prozessanalyse wurden die auffälligen Muster der fehlerhaften Produkte in dem Labor für Werkstoffkunde an der TH Köln, Campus Gummersbach untersucht, um ein umfassenderes Bild von den Fehlstellen zu bekommen. Diese Analysen gaben tiefe Einblicke in die Art der Mängel und lieferten erste Hinweise auf potenzielle Ursachen innerhalb der Produktionsschritte.

Ursachenforschung: Root Cause Analyse und Design of Experiments
Um die Ursache der Qualitätsprobleme zu identifizieren, führten wir eine umfassende Root Cause Analyse durch. Dieser Ansatz half dabei, die Ursachen einzugrenzen und potenzielle Problemquellen zu identifizieren. Anschließend wurde ein detailliertes Design of Experiments (DOE) entwickelt, um verschiedene Parameter gezielt zu testen und deren Auswirkungen auf die Produktqualität zu verstehen.
Diese strukturierte Vorgehensweise ermöglichte es, gezielt Änderungen in der Prozessführung einzuführen, die sich direkt auf die Fehlstellenrate und die allgemeine Qualität der Kunststofffolien auswirkten. Vor allem der Prozess des Anfahrens und der operative Betrieb wurden signifikant optimiert, was nicht nur die Qualität der Produkte, sondern auch die Effizienz der Produktion verbesserte.
Resultate: Verbesserungen in Betrieb und Qualität
Durch die enge Zusammenarbeit mit Gislaved Folie und die Anwendung von analytischen und systematischen Methoden wie Root Cause Analyse und DOE konnten wesentliche Prozessverbesserungen erzielt werden. Die Kalander-Anlage arbeitet nun effizienter, und die Fehlstellen in den Produkten wurden deutlich reduziert. Darüber hinaus wurde das Team von Gislaved Folie in den neuen Prozessen geschult, was die nachhaltige Umsetzung der Verbesserungen gewährleistet.
Nachhaltige Optimierung durch systematische Analyse
Dieses Projekt bei Gislaved Folie verdeutlicht, wie eine Kombination aus Value Stream Mapping, Root Cause Analyse und Design of Experiments zur Optimierung von Produktionsprozessen beitragen kann. Durch die systematische Analyse und die enge Zusammenarbeit mit den Mitarbeitern vor Ort konnten wir signifikante Verbesserungen in der Produktionsqualität und der Prozesseffizienz erreichen. Dies zeigt einmal mehr, wie wichtig ein strukturierter Ansatz in der Prozessoptimierung ist, um langfristige und nachhaltige Verbesserungen zu erzielen.
Gislaved Folie
Gislaved Folie ist ein führender Hersteller von hochwertigen Kunststofffolien, die in einer Vielzahl von Industrien Anwendung finden, darunter Automobil, Bauwesen und Verpackung. Das schwedische Unternehmen blickt auf eine lange Tradition in der Produktion von PVC- und Polyolefin-Folien zurück, die durch herausragende Qualität, Anpassungsfähigkeit und Nachhaltigkeit überzeugen. Gislaved Folie steht für innovative Lösungen, die auf die spezifischen Anforderungen der Kunden zugeschnitten sind, und bietet eine breite Palette von Produkten, die sowohl für technische als auch ästhetische Anwendungen geeignet sind. Das Unternehmen ist bekannt für seine Präzision und sein Streben nach kontinuierlicher Verbesserung, um den höchsten Qualitätsstandards gerecht zu werden.
TH Köln, Campus Gummersbach – Labor für Werkstoffe
Das Labor für Werkstoffe am Campus Gummersbach der Technischen Hochschule Köln bietet eine umfassende Plattform für Forschung und Lehre im Bereich der Werkstofftechnik. Im Mittelpunkt stehen die Untersuchung von Materialeigenschaften, Prüfverfahren und die Entwicklung neuer Werkstoffe für industrielle Anwendungen. Studierende und Forschende profitieren von modernster Ausstattung und der engen Verknüpfung von Theorie und Praxis. Das Labor spielt eine zentrale Rolle in der Ausbildung von Ingenieuren und Technikern und unterstützt Projekte, die sich auf die Optimierung von Materialien und Fertigungsverfahren konzentrieren. Durch seine anwendungsorientierte Ausrichtung trägt das Labor zur Lösung aktueller technischer Herausforderungen in der Industrie bei.
コメント